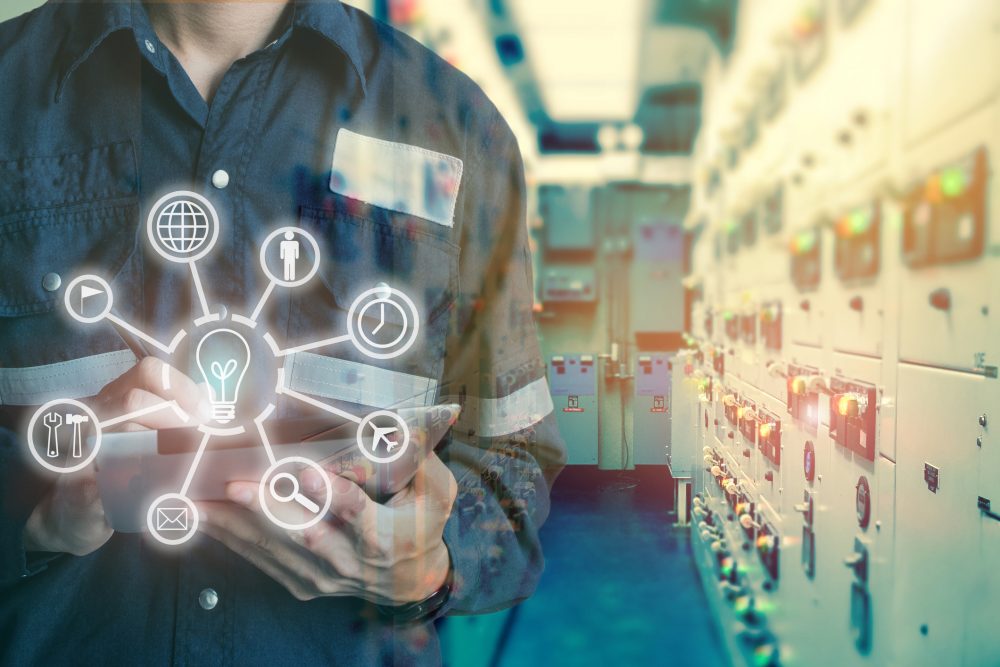
Instandhaltung 4.0: Predictive Maintenance
Die industrielle Instandhaltung der vierten Welle am Prüfstand: Technische Ausfälle und verminderte Produktionsqualität durch Verschleiß von Maschinen und Material führen in der Industrie zu massiv steigenden Kosten. Der Wandel von reaktiven zu präventiven Maßnahmen ist unumgänglich. Im Artikel lesen Sie über Potenziale, Herausforderungen und Praxisbeispiele.
Was ist Predictive Maintenance?
Unter Predictive Maintenance versteht man vorausschauende Instandhaltung – beispielsweise im Rahmen von Herstellungsprozessen. Die Wartung basiert dabei auf Maschinen- und Produktionsdaten in Echtzeit, die Auskunft über Anlagenzustand, Nutzungsdauer, Leistungsfähigkeit und Co. liefern. So können korrigierende Maßnahmen geplant und durchgeführt werden, bevor es zu kritischen Situationen kommt. Drohende Schäden oder auch völlige Produktionsausfälle lassen sich mit dieser Methode weitgehend verhindern.
Die Vorteile der vorausschauenden Instandhaltung
- Mit vorausschauender Instandhaltung werden selbst kleine Missstände oder Qualitätsabfälle in der Produktion rasch sichtbar und können unmittelbar behoben werden. Ungeplante Stillstände oder gar Maschinenausfälle durch Defekte und Beschädigungen von Anlagen können so weitgehend vermieden werden. Das spart langfristig Kosten ein und sichert die Herstellungsprozesse ab.
- Regelmäßig gewartete Maschinen besitzen eine höhere Lebensdauer. Da die Anschaffung neuer Anlagen und Geräte besonders kostenintensiv ist, wirkt sich die langjährige Nutzung von bereits vorhandenen Maschinen deutlich positiv auf das Budget aus.
- Für hochwertige Wartung und umfassenden Service wird geschultes Personal benötigt. Auch dieser Ressourcenaufwand wird durch Predictive Maintenance besser planbar. Die Mittel zur Instandhaltung können daher effizient genutzt werden, und der ideale Zeitpunkt für Servicearbeiten wird konkret bestimmt.
- Auch beim Ersatzteil-Management werden Kosten eingespart: Durch die regelmäßige Datenerhebung steigt auch die Planbarkeit beim Bedarf an Ersatzteilen samt deren Beschaffung. Lagerstände lassen sich dadurch besonders effizient auffüllen, was sich auf die benötigte Größe von Lagerhallen auswirken kann.
- Die gesammelten Daten sind außerdem für einen weiteren Zweck nützlich: für die Prozessoptimierung. Die Datensätze ermöglichen Rückschlüsse auf die Effizienz von Abläufen und die Leistung von Anlagen. Daraus resultierende Verbesserungen auf Basis der Datenanalyse führt zu einer höheren Produktivität.
Die Herausforderungen der vorausschauenden Instandhaltung
Für erfolgreiche Predictive Maintenance sind immense Datenmengen (Big Data) nötig – um zuverlässige Aussagen machen zu können und damit verbunden relevante Einschätzungen für Planungen zu geben. Sie kommen in den unterschiedlichsten Formen und Einheiten vor. Beispielsweise werden Schwingungen oder Vibrationen, Töne und Lautstärkepegel, Temperaturen, Flüssigkeitsmengen, Füllstände, Leitfähigkeit, Feuchtigkeitsstufen oder auch Verunreinigungsgrade miteinbezogen. In dieser Aufgabe liegen auch die meisten Hürden der vorausschauenden Instandhaltung:
- Die Sammlung und Verarbeitung der riesigen Informationsmengen ist in der Praxis für viele Unternehmen nicht stemmbar. Vor allem das Filtern nach relevanten und irrelevanten Daten stellt eine große Herausforderung dar.
- Für die Datenerhebung bedarf es zudem spezieller Analyse- und Überwachungstools. Beispielsweise sind feinfühlige Sensoren und ausreichend digitale Schnittstellen unabdingbar. Sind die Maschinen dafür noch nicht vorhanden oder bereits etwas in die Jahre gekommen, müssen sie nachgerüstet werden, was kurzfristig zu hohen Ausgaben führt. Auch diese Anlagen benötigen regelmäßige Inspektion und Wartung – ein weiterer Kostenfaktor!
Und weil selbst die innovativsten Prozesse nicht völlig autonom funktionieren, darf auch das Fachpersonal nicht vergessen werden, welches sich mit den Abläufen und Aufgaben rund um Predictive Maintenance auseinandersetzt – vom Programmierer bis hin zum Elektriker vor Ort.
Predictive Maintenance: Die Funktionsweise
Ein primärer Bestandteil von Predictive Maintenance ist die Zustandsüberwachung. Dabei handelt es sich um das kontinuierliche Einholen von großen Mengen unterschiedlicher Daten durch Systemüberwachungen und Messungen und den anschließenden Abgleich mit älteren Werten.
KI-unterstützte Mechanismen erleichtern den Umgang mit Big Data. Systemen wird dabei durch Machine-Learning beigebracht, wie bestimmte Parameter, Faktoren und Umwelteinflüsse miteinander korrelieren und welche Schlüsse daraus zu welchen Zeitpunkten zu ziehen sind. Je mehr Daten gesammelt werden, desto komplexer und spezifischer werden die Rückschlüsse und Zusammenhänge, die das System auswirft. Mit jedem neuen Szenario tun sich neue Erkenntnisse auf, von denen die vorausschauende Instandhaltung künftig profitieren kann.
Predictive Maintenance: Die Anwendungen
Zahlreiche Industriefelder haben Predictive Maintenance bereits für sich entdeckt. Besonders beliebt ist der Einsatz der Methodik auf den folgenden Gebieten:
- Windkrafttechnologie: Sensoren in Motor oder Fahrwerk zeigen kleine Defekte auf und verhindern kostspielige Totalausfälle.
- Moderne Kfz-Wartung & E-Mobilität: Intelligente, vernetzte Autos leiten Defekte und andere relevante Infos über den Fahrzeug-Zustand selbstständig und unmittelbar an den Hersteller weiter, wodurch Modell- oder Chargenfehler schneller entdeckt und behoben werden können. Bei Elektrofahrzeugen wird die Methode für die Zustandsbewertung und Prognosen über die Akkubeschaffenheit genutzt.
- Flugzeugtechnologie: Dass frühzeitige Fehlererkennung in der Luftfahrt essenziell ist, liegt auf der Hand. Wenn Flugzeuge wegen längerer Wartungsarbeiten nicht abheben können, verursacht dies weitreichende Kettenreaktionen bei den Airlines und enorme Kosten.
- Schienenwartung: Auch beim Schienenverkehr können durch Predictive Maintenance Störungen und Verzögerungen im laufenden Betrieb verhindert werden: Spurlücken werden rasch erkannt und schadhafte Weichen ausgetauscht.
- Energieversorgung: Um eine durchgängige Stromversorgung gewährleisten zu können, sind Frühwarnzeichen für Versorgungsdienstleister besonders wichtig. Intelligente Systeme erkennen in Echtzeit Differenzen zwischen Angebot und Nachfrage und ermöglichen ein schnelles Handeln innerhalb der Branche.
- Öl- und Gasbranche: Wenn sich Gerätschaften und Ausrüstung zur Öl- und Gasraffinerie an Tiefwasserstandorten befinden, lässt sich ihr Zustand mit klassischen Wartungsansätzen nur schwer abschätzen. Predictive Maintenance ermöglicht gleichbleibende Qualitätsstandards und eine erhöhte Lebensdauer der eingesetzten Maschinen.
- Diverse Produktionsbetriebe: Auch in Rahmen von klassischen Herstellungs- und Fertigungsprozessen entstehen bei verspäteten Reparaturen oft große Schäden betreffend den Produktionsablauf und die Qualität der Produkte. Hohe Kosten und wirtschaftliche Einbußen sind die Folge.
Instandhaltung 4.0: Wartung, statt warten!
Predictive Maintenance hat in diversen Branchen bereits einen hohen Stellenwert erreicht – das Potenzial ist aber noch nicht zur Gänze ausgeschöpft. Der Umgang mit Big Data stellt dabei eindeutig die größte Herausforderung dar. Die Entwicklungen und Prognosen sind jedoch vielversprechend, und der Grundtenor lautet: Wartung, statt warten!
Predictive Maintenance wird sich auch zukünftig immer stärker durchsetzen. Voraussetzung für eine erfolgreiche Nutzung und Etablierung ist und bleibt aber, dass sowohl die technischen als auch personellen Ressourcen zur Erhebung und Verarbeitung der immensen Datenmengen gegeben sind. Es empfiehlt sich daher ein langsames Herantasten an die Materie, anstatt den gesamten Wartungsbereich gleich mit einem Satz umstellen zu wollen. Das bewahrt vor Überraschungen, sollten die Aufwandschätzungen hinsichtlich Zeit, Personal oder Kosten doch nicht gänzlich mit der Realität übereinstimmen. Eines aber ist klar: Langfristig führt kein Weg an Predictive Maintenance vorbei.
Sie wollen noch mehr Konkretes aus der Thematik Industrie 4.0 erfahren? Dann klicken Sie sich durch unsere Kategorie Industrie 4.0, in der wir beispielsweise der Traceability bei Produktionsprozessen auf den Grund gehen oder uns mit dem Einsatz von RFID-Komponenten befassen. Jetzt online lesen und Neues erfahren! Erfahren Sie außerdem mehr zu Produkten für eine erfolgreiche MRO-Strategie.