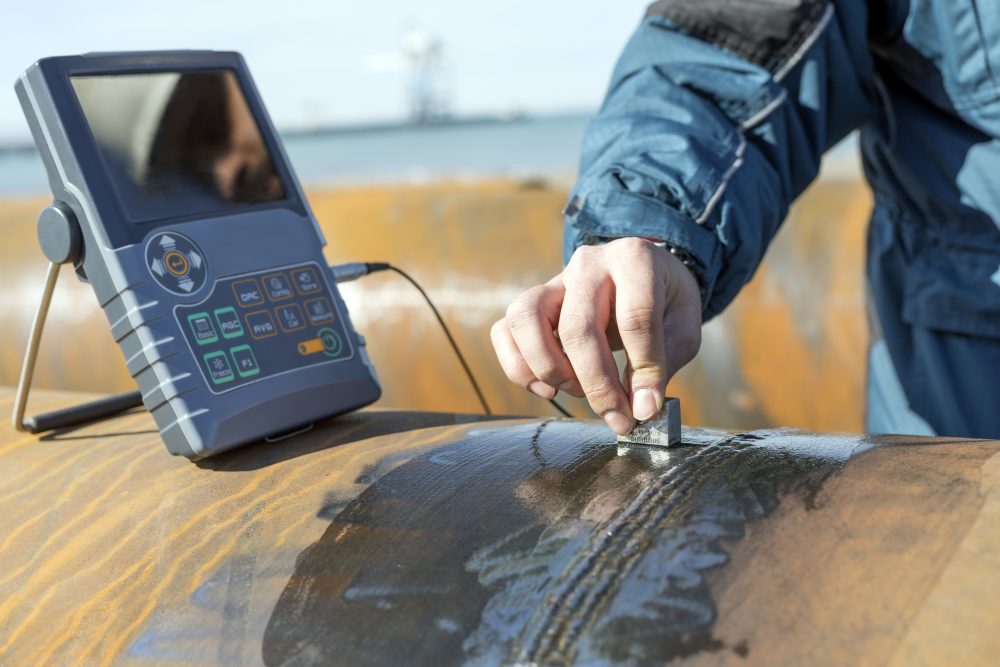
Ultraschallprüfung (UT) und -sensoren in der Industrie
Die Ultraschallprüfung und -sensoren spielen in der Industrie eine wichtige Rolle bei der Fehlerermittlung von Werkstücken. Doch wie funktioniert eine Ultraschallprüfung überhaupt? In unserem Artikel erfahren Sie nicht nur die Grundlagen der UT-Prüfverfahren, sondern auch wann und warum eine Schallwelle reflektiert wird. Lesen Sie weiter und entdecken Sie, wie diese Technologie dazu beiträgt, die Qualität von Produkten zu verbessern.
Inhaltsverzeichnis
Eine Ultraschallprüfung ist eine effektive Methode, um Materialfehler in elektronischen Bauteilen oder Werkstücken zu ermitteln. Aber auch in anderen industriellen Bereichen werden Prüfverfahren mittels Ultraschallsensoren durchgeführt. Über das Gerät wird ein akustisches Signal in das zu prüfende Objekt gesendet, welches diese gesendeten Ultraschallwellen Signal sodann reflektiert. In der Folge lassen sich Fehler identifizieren, Entfernungen messen, Füllstände in Tanks überwachen und relevante Informationen erfassen.
Wie funktioniert eine Ultraschallprüfung?
Eine Überprüfung mittels Ultraschall funktioniert nach folgendem Prinzip: Im Sensorteil des Prüfgerätes befindet sich eine piezoelektrische Scheibe, die einen Ultraschallimpuls senden und empfangen kann. Das Ultraschallprüfgerät sendet den Schallwellenimpuls in das Werkstück. Der Schall durchläuft dieses und wird an der Rückwand des Objektes reflektiert.
Dadurch können unterschiedliche Informationen (zum Beispiel Füllstände, Beschädigungen oder Abstände) auf Basis der gemessenen Schallwellen erfasst und ausgewertet werden. Wichtig ist dabei eine besonders hohe Messgenauigkeit.
Messgenauigkeit von Ultraschallsensoren
Die Funktion von Ultraschallsensoren kann durch unterschiedliche Umgebungseinflüsse beeinträchtigt werden. Dazu zählen die Lufttemperatur, Luftfeuchtigkeit, Druck, Luftströmungen oder Fremdschall. Den größten Einfluss auf die Messung nimmt die Temperatur.
Ein Ultraschallsensor arbeitet nach dem Echo-Laufzeitverfahren. Es wird der zeitliche Abstand zwischen dem gesendeten Impuls und dem Echo ausgewertet. So können beispielsweise Entfernungen oder Beschädigungen ermittelt werden. Bei der Schallausbreitung in der Umgebungsluft beträgt die Schallgeschwindigkeit zum Beispiel 344 Meter pro Sekunde – bei Raumtemperatur. Sie ist mit rund 0,17 Prozent pro Grad Celsius temperaturabhängig. Die Folge: Die vom Ultraschallsensor gemessene Laufzeit und die berechnete Entfernung wird verfälscht.
Um diesen Effekt auszugleichen, empfehlen sich Sensoren mit integriertem Temperaturfühler. Unter den Ultraschallsensoren der Marke Pepperl+Fuchs empfiehlt sich dafür beispielsweise das Modell UB400-12GM. Bei dessen Anwendung können Messabweichungen durch die Umgebungstemperatur ausgeglichen werden.
Ultraschall zur Fehlerermittlung in Werkstücken
Ultraschall kann auch für die Suche nach Beschädigungen genutzt werden, wobei Risse, Lunker oder Einschlüsse in einem Werkstück gefunden werden können. Bei der Prüfung eines fehlerfreien Objektes durchströmt der Impuls das Gerät oder Werkstück vollständig. Falls Fehler vorhanden sind, wird der Impuls teilweise reflektiert. Ein Teil des Signals kommt also früher am Sender-Empfänger-Gerät an als der Rest.
Über ein mit dem Ultraschallprüfgerät gekoppeltes Display können die Dichte (Y-Achse) und die Tiefe (X-Achse) des Werkstückes abgebildet werden. Um das Verfahren durchführen zu können, wird ein Koppelmittel auf die zu prüfende Komponente aufgetragen. So lassen sich Beschädigungen oder Schwachstellen im Werkstück identifizieren, ohne dass das elektronische Gerät oder Bauteil „zerstört“ werden muss.
Weitere Anwendungsbereiche von Ultraschallwellen in der Industrie
- Kontaktlose Füllstandmessung
- Ultraschall-Dichtemessung
- Materialbearbeitung
- Informationsverarbeitung und -übertragung
- Werkstoffprüfung und Strukturuntersuchung
- Abstandsmessung und -regelung
- Bahnkantensteuerung
- Höhenabtastung
Grundlagen der Ultraschallprüfung: Welche Prüfverfahren gibt es?
Bei der Ultraschallprüfung gibt es mehrere Verfahrensmethoden: Dazu zählen unter anderem das Impuls-Echo-Verfahren, das Durchschallungsverfahren und weitere Sonderprüfverfahren. Diese lassen sich wiederum in unterschiedliche Messungs- und Auswertungsmethoden unterteilen. Bürklin Elektronik stellt Ihnen die drei genannten Prüfverfahren vor:
Durchschallungsverfahren
Beim Durchschallungsverfahren befindet sich das Werkstück zwischen dem Sender des Impulses und dem Empfängerteil. Das Signal wird gesendet und bei fehlerfreier Struktur fast vollständig an den Empfänger übermittelt. Liegt ein Fehler vor, wird das Signal nur teils oder gar nicht empfangen.
Bei diesem Verfahren kann nicht die Tiefe bzw. Position des Fehlers ermittelt werden. Daher eignet es sich nur für Bauteile mit parallelen Begrenzungen. Ideal ist die Anwendung bei dünnen Bauteilen (zum Beispiel Platinen) und bei der Fehlerermittlung direkt unter der Oberfläche eines Werkstückes.
Impuls-Echo-Verfahren
Beim Impuls-Echo-Verfahren befinden sich Sender und Empfänger im Prüfkopf des Ultraschallmessgerätes. Dabei werden kurze (zeitlich begrenzte) Schallimpulse an das Werkstück gesendet. Anfangs sind diese als Sendeimpulse auf dem Display erkennbar.
Ist der Prüfkörper (= Werkstück) fehlerfrei, werden die Impulse von der Rückwand des Werkstückes reflektiert – das bezeichnet man als Rückwandecho. Ist ein Fehlerenthalten, wird das Signal wieder früher an den Prüfkopf gesendet. Die beschädigte Stelle ist auf dem Display erkennbar.
Sonderprüfverfahren
Unter den Bereich der Sonderprüfverfahren fallen mehrere unterschiedliche Verfahrensweisen, wie etwa das Phased-Array-Verfahren, das TOFDD-, Guided-waves- oder LORUS-Verfahren. Anstatt Fehlerstellen zu suchen, wird beispielsweise eine Multizonenprüfung durchgeführt: Untersucht werden dabei ausgewiesene Bereiche im Werkstück – in einem definierten, zu prüfenden Bereich.
Ultraschallprüfung: Wann und warum wird eine Schallwelle reflektiert?
Eine Ultraschallwelle wird dann reflektiert, wenn sie von einer Oberfläche zurückgeworfen wird. Der Schallwiderstand ist nach folgender Formel zu berechnen: Schallwiderstand = Dichte x Schallgeschwindigkeit.
Der Schall breitet sich im Werkstück mit der spezifischen Schallgeschwindigkeit so lange aus, bis er auf eine Änderung/Anomalie des Schallwiderstandes (= Schallkennimpedanz) trifft. An der Grenzfläche wird der Schall dann reflektiert, weil der Schallwiderstand von beispielsweise Luft geringer ist als der von Stahl.
Definition von Schallkennimpedanz: eine physikalische Größe, die sich aus dem Verhältnis von Schalldruck (=p) zu Schallschnelle (v) ergibt. ZF = p/v.
Um eine korrekte Messung durchführen zu können, braucht es eine Kopplungsflüssigkeit zwischen Prüfkopf und Werkstück. Die Flüssigkeit dient dazu, die minimalen Unebenheiten am Werkstück auszugleichen. Grund: Ohne die Kopplungsflüssigkeit würde der Schall direkt an der Oberfläche reflektiert werden. Ein Prüfergebnis könnte nicht ermittelt werden.
Gut zu wissen: Die Vertiefungen an der Oberfläche eines zu prüfenden Stückes dürfen nicht tiefer als 10-7 Millimeter sein. Ansonsten können die Ultraschallwellen nicht in das Werkstück eindringen.
Grundvoraussetzung: Größe und Breite des Fehlerbereiches
Um einen Fehler in einem Werkstück messen zu können, muss dieser größer sein als die halbe Wellenlänge Lambda des darauf treffenden Schalls. Die Wellenlänge errechnet sich aus der Schallgeschwindigkeit (c) geteilt durch die Schallfrequenz (f).
Je kleiner der zu messende Fehler, desto größer muss die Ultraschall-Frequenz (= f) gewählt werden. Grund dafür ist, dass die halbe Wellenlänge kleiner bleiben muss als die Fehlerbreite.
Ein Rechenbeispiel zur Berechnung der Ultraschallfrequenz
Mit einem Rechenbeispiel soll verdeutlicht werden, wie ein Ultraschall-Prüfkopf justiert werden muss, um ein Prüfergebnis ausgeben zu können. Folgende Annahme: Geprüft wird ein Werkstück aus Stahl, mit der anzunehmenden Ultraschallgeschwindigkeit von c = 5.920 Meter pro Sekunde. Angenommen wird, dass sich ein Fehler im Material befindet, der eine Fehlerbreite von 1,5 Millimetern aufweist.
Die für das Beispiel festgelegte Wellenlänge ist mit Lambda 3,0 Millimeter ausgegeben, da diese kleiner sein muss als die Fehlerbreite. Die für eine Messung erforderliche Schallfrequenz ergibt sich durch die Division der Schallgeschwindigkeit durch die Wellenlänge: f = c / ƛ.
f = 5.920 / 3,0 – das Ergebnis ist eine Schallfrequenz von 1,97 Megahertz. Das bedeutet, dass mindestens eine Schallfrequenz von 1,97 MHz gewählt werden muss, um Fehler von 1,5 Millimetern Breite im Werkstoff Stahl (gerade) noch erkennen zu können.
Akustische Materialeigenschaften
Metalle | Schallgeschwindigkeit (Longitudinalwelle) cl [m/s] | Schallgeschwindigkeit (Transversalwelle) cl [m/s] | Dichte [103 kg/m3] | Akustische Impedanz [106 kg/m2s] |
---|---|---|---|---|
Aluminium | 6200 – 6360 | 3100 – 3130 | 2,7 | 16,7 – 17,2 |
Beryllium | 12720 – 12890 | 8330 – 8880 | 1,82 – 1,87 | 23,2 – 24,1 |
Blei | 2050 – 2400 | 700 – 710 | 11,3 – 11,7 | 23,2 – 28,1 |
Eisen | 5950 | 3220 – 3240 | 7,9 | 47,0 |
Gold | 3240 | 1200 | 19,7 | 63,8 |
Grauguss | 3500 – 5600 | 2200 – 3200 | 7,2 | 25,2 – 40,3 |
Gusseisen | 3500 – 5800 | 2200 – 3200 | 6,9 –7,3 | 24,2 – 42,3 |
Hartmetall | 6800 – 7300 | 4000 – 4700 | 11,0 – 15,0 | 74,8 – 109,5 |
Kadmium | 2665 – 3300 | 1500 – 1810 | 8,6 – 8,7 | 22,9 – 28,5 |
Konstantan | 5240 | 2640 | 8,8 | 46,1 |
Kupfer | 3666 – 4760 | 2260 – 2320 | 8,9 | 32,6 – 42,4 |
Magnesium | 4602 – 5900 | 3050 – 3280 | 1,70 – 1,75 | 7,8 – 10,3 |
Messing (Ms58) | 3830 – 4250 | 2050 – 2200 | 8,1 | 31,0 – 34,4 |
Molybdän | 6250 – 6650 | 3350 – 3510 | 10,1 – 10,2 | 63,1 – 67,8 |
Nickel | 4973 – 6040 | 2960 – 3219 | 8,8 – 8,9 | 43,8 – 53,8 |
Platin | 3960 – 4080 | 1670 – 1730 | 21,4 | 84,7 – 87,3 |
Silber | 3600 – 3790 | 1590 – 1690 | 10,4 | 37,4 – 39,4 |
Titan | 5823 – 6260 | 2920 – 3215 | 4,5 | 26,2 – 28,2 |
Zink | 3890 – 4210 | 2290 – 2440 | 7,1 | 27,6 – 29,9 |
Zinn | 3210 – 3320 | 1530 – 1670 | 7,3 | 23,4 – 24,2 |
Nichtmetalle | Schallgeschwindigkeit (Longitudinalwelle) cl [m/s] | Schallgeschwindigkeit (Transversalwelle) cl [m/s] | Dichte [103 kg/m3] | Akustische Impedanz [106 kg/m2s] |
---|---|---|---|---|
Aluminiumoxid | 9000 – 11000 | 5500 – 6500 | 3,6 – 3,95 | 32,4 – 43,5 |
Eis (H2O bei -4 °C) | 3232 – 3980 | 1990 | 0,9 | 2,9 – 3,6 |
Epoxydharz | 2400 – 2900 | 1100 | 1,1 – 1,25 | 2,64 – 3,63 |
Glas (Fensterglas) | 5770 | 3430 | 2,51 | 14,5 |
Glas (Quarzglas) | 5570 – 5930 | 3415 – 3750 | 2,6 | 14,5 – 15,4 |
Graphit, gepresst | 1600 – 2500 | 1200 – 1500 | 1,7 – 2,3 | 2,72 – 5,8 |
Gummi, hart | 1570 – 2300 | – | 1,2 | 1,88 – 2,76 |
Gummi, weich | 1480 – 1550 | – | 0,90 – 0,95 | 1,33 – 1,47 |
PA (Polyamid) | 1800 – 2600 | 1100 – 1200 | 1,1 – 1,2 | 1,98 – 3,12 |
PE (Polyethylen) | 1950 – 2000 | 540 | 0,9 | 1,76 – 1,80 |
PMMA (Plexiglas®) | 2670 – 2760 | 1120 – 1430 | 1,18 | 3,2 – 3,3 |
Porzellan | 5600 – 6200 | 3500 – 3700 | 2,4 – 2,5 | 13,4 – 15,5 |
Polystyrol | 2337 – 2350 | 1020 – 1150 | 1,05 – 1,06 | 2,45 – 2,49 |
PVDF (Polyvinyliden-fluorid) | 2200 | 775 | 1,78 | 3,9 |
PTFE (Teflon®) | 1350 | 550 | 2,2 | 2,97 |
PVC (Polyvinylchlorid) | 2180 – 2260 | 948 | 1,38 – 1,40 | 3,0 – 3,2 |
Quarzkristall | 5760 | 3840 | 2,65 | 15,2 |
Stahl | Schallgeschwindigkeit (Longitudinalwelle) cl [m/s] | Schallgeschwindigkeit (Transversalwelle) cl [m/s] | Dichte [103 kg/m3] | Akustische Impedanz [106 kg/m2s] |
---|---|---|---|---|
Baustahl, unlegiert bis 0,2 % C, z. B. St 52-3 n. DIN 54120 | ||||
- geglüht | 5890 – 5950 | 3240 – 3270 | 7,85 | 46,2 – 46,7 |
- bis 0,5% C geglüht | 5940 – 5960 | 3230 – 3245 | 7,8 – 7,85 | 46,3 – 46,8 |
Baustahl, legiert (0,35 % C, 0,6 % Mn, 1 % Cr, 0,2 % Mo) | ||||
- geglüht | 5950 | 3260 | 7,84 | 46,6 |
- vergütet | 5930 | 3240 | 7,84 | 46,5 |
- gehärtet | 5900 | 3230 | 7,84 | 46,3 |
Baustahl, legiert (0,3 % C, 0,4 % Mn, 2 % Cr, 2 % Ni, 0,2 % Mo) | ||||
- geglüht | 5930 | 3220 | 7,85 | 46,6 |
- vergütet | 5870 – 5880 | 3210 | 7,85 | 46,1 – 46,2 |
- gehärtet | 5890 | 3210 | 7,85 | 46,2 |
Kugellagerstahl (1 % C, 1,5 % Cr) | 5990 | 3270 | 7,8 | 46,7 |
Rostfreier Stahl, austenitisch | ||||
- (X 10 Cr Ni 18 8) geglüht | 5530 | 2983 | 7,9 | 43,7 |
- (X 10 Cr Ni Nb 18 9) | 5790 | 3100 | 7,8 – 7,9 | 45,2 – 45,7 |
- (X 12 Cr Ni 18 8) | 5660 | 3120 | 7,8 | 46,3 – 47,5 |
Rostfreier Stahl, ferritisch (0,15% C, 17% Cr) - geglüht | 6010 | 3360 | 7,7 – 7,9 | 46,3 – 47,5 |
Schnellstahl (0,9% C, 4 % Cr, 2,5 % Mo, 2,5 % V, 3 % W) | ||||
- geglüht | 6060 | 3850 | - | - |
- gehärtet | 5880 | 3190 | - | - |
Werkzeugstahl (1 % C) | ||||
- geglüht | 5940 – 5960 | 3220 – 3245 | 7,8 – 7,84 | 46,3 – 46,7 |
- gehärtet | 5854 | 3150 | 7,84 | 45,9 |
Werkzeugstahl (2 % C, 12 % Cr, 0,6 % W) | ||||
- geglüht | 6140 | 3310 | 7,75 – 7,8 | 47,6 – 47,9 |
- gehärtet | 6010 | 3220 | 7,75 | 46,6 |
Ultraschallsensoren für die Industrie bei Bürklin Elektronik
Industrielle Ultraschallsensoren sind aus zahlreichen Industriebereichen nicht mehr wegzudenken. Sie erfüllen unterschiedlichste Aufgaben und Funktionen, beispielsweise Informationserfassung und -verarbeitung. Dazu müssen sie höchsten technischen Anforderungen entsprechen.
Abgesehen vom effizienten Ausgleich thermischer Schwankungen, die den Messvorgang beeinflussen, sollten Ultraschallsensoren zuverlässig und präzise arbeiten. Entsprechend dem jeweiligen Einsatzgebiet müssen Sensoren über spezifische Eigenschaften verfügen. Etwa im Erfassungsbereich, wo Sensoren für die Überprüfung von großen Bauteilen in Produktionsstraßen Eingesetzt werden.
Produkt-Empfehlung:
- der Ultraschallsensor UC4000 der Marke Pepperl+Fuchs mit einem regulierbaren Erfassungsbereich von 200 bis 4.000 Millimetern oder der
- Sensor von Pepperl+Fuchs mit drehbarem Sensorkopf.
Auch Sensoren mit einer kleiner Blindzone – Bereich direkt vor dem Sensor, der nicht erkannt wird – steigern die Effizienz des Prüfverfahrens. Denn: Je schneller das zu erfassende oder prüfende Objekt erkannt wird, desto reibungsloser kann die Produktionsanlage beziehungsweise Maschine arbeiten.
Bürklin Elektronik bietet ein umfangreiches Spektrum an hochwertigen Ultraschallsensoren für zahlreiche Industrieanwendungen. Jetzt das Produktportfolio kennenlernen!