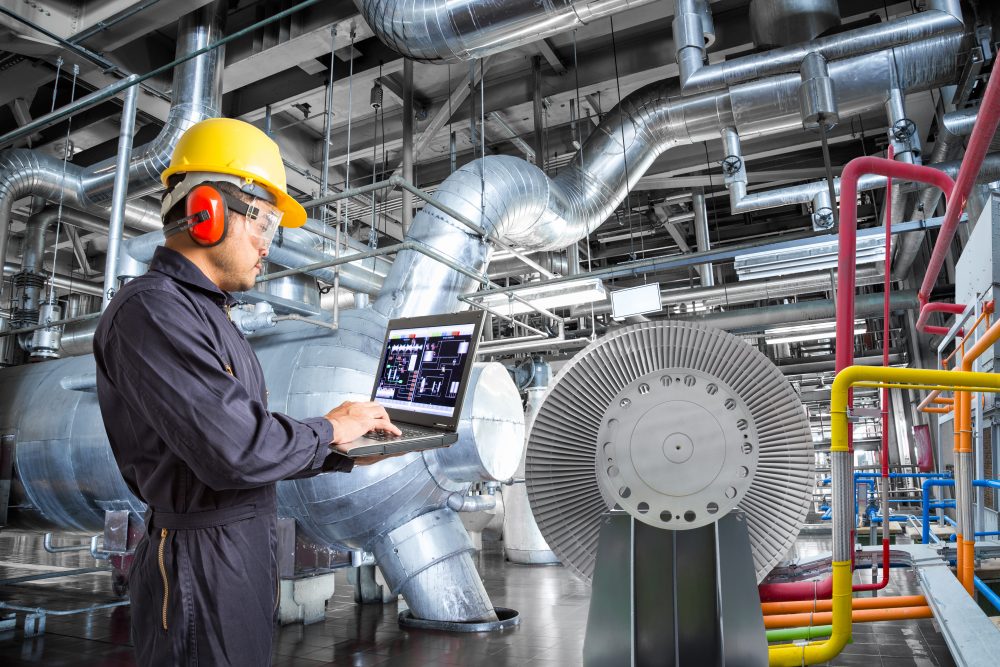
DIN 31051: Fundamentals of Maintenance
Keeping technical facilities in good shape when it comes to their efficiency, operational safety and longevity requires careful maintenance. The standard DIN 31051 offers a structured approach to effective maintenance and improvement of objects through four clearly defined measures. We break down the profitable topic in detail for you.
Table of contents
- Definition DIN 31051
- Maintenance according to DIN 31051 - Prevention through regular checks
- Inspection according to DIN 31051 - Check-up for electronics
- Repair according to DIN 31051 - Fixing of defects
- Improvement according to DIN 31051 - Optimization of functional capability
- Classification by DIN EN 13306
- Benefits and future developments of maintenance
Definition DIN 31051
Maintenance according to DIN 31051 is a central pillar of quality assurance. It describes the sum of measures related to the technical, organizational and administrative maintenance of the quality of a component or machine. Standardized maintenance minimizes downtimes and prevents expensive repairs or replacements. This approach is therefore essential, especially for the electronics industry, where precision and reliability are crucial. In the measures described, the DIN 31051 standard can be divided into maintenance, inspection, repair and improvement.
Maintenance according to DIN 31051 – Prevention through regular checks
In the area of maintenance, everything primarily revolves around ensuring that the target condition is maintained and that operational reliability is intact. This includes preventive measures such as oiling and greasing components, refilling operating materials and replacing wear parts. The focus is always on prevention and delaying signs of wear, as these inevitably cause costs. Continuous maintenance leads to the avoidance of extensive repairs and ensures the long-term functionality of technical components. Regular cleaning and adjustment of microchips, for example, are classic maintenance tasks in the electronics industry. In semiconductor production, this ensures the high standards of quality and reliability.
Inspection according to DIN 31051 – Check-up for electronics
In order to be able to act quickly and purposefully in the event of unexpected problems, regular thorough inspections of the condition of a technical object are necessary. In the course of the inspection, the current condition of a maintenance object can be ascertained, recorded and subsequently assessed using a variety of techniques. Depending on the industry and the property to be inspected, a wide variety of methods are used and uncover potential sources of defects even before damage actually occurs. In printed circuit board manufacturing, for example, print quality is monitored using automated optical inspection (AOI).
Repair according to DIN 31051 – Fixing of defects
Efficient prevention of defects is always desirable, but if damage and malfunctions have already occurred, it is important to repair them quickly by means of repair measures. Prevention includes any repair measures to restore an object to its defined target condition. In many cases, this involves replacing faulty or completely defective components. Particularly in the telecommunications sector, it is well known what far-reaching consequences the failure of network components can cause. In order to avoid image damage due to long downtimes and to restore stable operation of the network, reliable and fast repair is essential.
Improvement according to DIN 31051 – Optimization of functional capability
If there are no defects to be repaired, another component of maintenance according to DIN 31051 comes into play with the improvement measure. The aim here is to adjust functioning systems and equipment so that they work even more efficiently and reliably. These fine adjustments can result in increases in economic efficiency, production reliability and environmental compatibility. Weak point analyses identify the production sections in systems that are functioning but whose maximum efficiency has not yet been fully exploited. Such measures are typical in the continuous improvement of automated production lines, such as in the manufacture of printed circuit boards.
Classification by DIN EN 13306
In addition to the classic DIN 31051, another standard is relevant in connection with maintenance: DIN EN 13306. In this standard, the individual measures are divided into two overriding main categories, namely predictive and corrective maintenance. Although they tie in at different points in the overall maintenance process, they only achieve the desired effect in combination with each other.
Predictive maintenance
Predictive maintenance covers all work steps that identify potential failures and defects at an early stage before they occur. Specifically: maintenance and inspection. Particularly in medical technology, sensitive sensors and the circuits of complex systems require this proactive approach for reliable quality assurance.
Corrective maintenance
Corrective maintenance is the elimination of faults after malfunctions and failures that occur despite preventive measures – in other words, repair. This can be explained by looking at the repair of defective microchips in computer hardware. After all, although preventive measures have been taken to minimize susceptibility to defects, occasional malfunctions are inevitable. Replacing the defective chip is therefore a repair measure that can be classified as corrective maintenance.
Are you still looking for suitable semiconductors and active components? At Bürklin Elektronik you can expect a wide range of products of the highest quality!
Benefits and future developments of maintenance
Let’s summarize: The maintenance standards DIN 31051 and DIN EN 13306 are decisive for quality assurance in the electronics industry. They ensure maximum uptime and increase the service life of equipment and machines. Substantial cost savings can be achieved as a result. The growing importance of the Internet of Things (IoT) and the increasing automation of various technical processes are currently resulting in significant developments in the area of maintenance. Concepts such as Maintenance 4.0 and Predictive Maintenance are playing an increasingly important role and enable intelligent, predictive maintenance – a clear step forward in terms of plant performance and efficiency.
Selected industry knowledge from the professionals
Focus your attention on current topics and trends in the industry with Bürklin Elektronik! In our online magazine “Electronic Competence”, we provide you with detailed insights into the areas of maintenance, energy efficiency, electronics manufacturing and Industry 4.0 as well as medical and measurement technology. Start browsing right away!