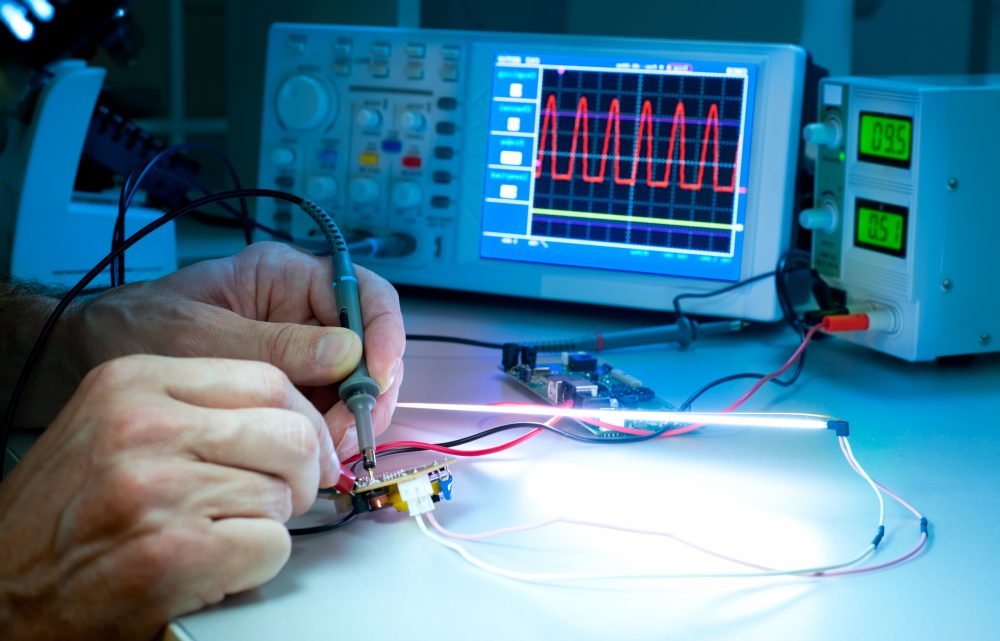
Inspection Techniques in Electrical Engineering
Inspection techniques in electrical engineering are indispensable for ensuring the safety and functionality of electrical systems. But what methods are there and how can they be used effectively? In our article, we give you an overview of the most important inspection techniques and show you how to detect and eliminate faults at an early stage.
If you want to work economically in electrical engineering, the systems and manufacturing processes used must be continuously subjected to tests and measurements. As a component of maintenance, inspection serves to identify any faults and defects at an early stage. A variety of different testing methods are used to analyze and assess the actual condition of materials, machines and components. Inspection techniques help to prevent production downtimes caused by component failures or system faults. Depending on the industry, the application area and the product to be inspected, various inspection techniques are used.
Visual inspection
Visual inspection is a purely optical check of an object or several components by sight. Electronic systems are checked for completeness and integrity either directly optically or by intelligent imaging sensors. Visible defects, impurities or construction errors can be detected. The method is used in the electronics industry, for example in the manufacturing of printed circuit boards and electronic assemblies. In industries such as food, cosmetics and pharmaceuticals, it is also used to inspect closures, fill levels, markings, package integrity and protective housings. Visual inspection can help ensure high quality standards. It also helps reduce corrections and rejects so that production processes remain efficient.
What is a Manual Optical Inspection (MOI)?
MOI involves inspection with the naked eye, or the inspecting person uses a microscope. Reference products are also repeatedly used for comparison – a proven technique, but one that has its limitations. The subjective perception of humans leads to inaccurate results. A risk factor is human error due to fatigue. The high time expenditure due to the slow working speed also makes the procedure only of limited use.
What is AOI inspection?
In Automatic Optical Inspection (AOI), a machine replaces human labor and independently inspects the respective components for defects using high-resolution cameras. Corresponding software algorithms create the basis for the quality assessment. The inspection delivers reproducible results at a consistently high quality and speed. AOI systems are preferably used in production processes with increased complexity.
Thermal inspection
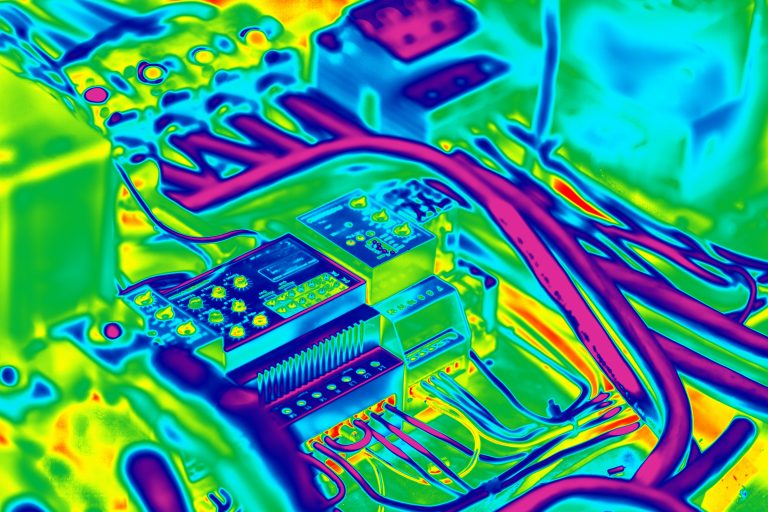
Another way to check electrical installations and systems for proper operation is through thermography. Temperature sensors and indicators quickly and efficiently show when a component or equipment unit is about to overheat. This allows faults to be detected more quickly and rectified before they degenerate into more serious malfunctions. Thermal imaging cameras are also frequently used in thermal inspection. They are used to locate hotspots, i.e. areas where excessive temperatures prevail. This is exactly where performance can be optimized to minimize the risk of overheating.
Insulation measurement and monitoring
If current flows in an electrical system, it must be ensured that it flows only in the intended conductors in order to protect against damage to property and personal injury. Perfect insulation is a basic prerequisite for this. Switches, pushbuttons and fuses are also affected by this. Insulation measurement involves determining the insulation resistance, which allows conclusions to be drawn about the integrity of the insulation and the potential existence of defective current flows. Prior to commissioning an electrical system, this test is referred to as insulation measurement. For later checks, while the systems are already running, it is called insulation monitoring.
Conductivity test
In addition to intact insulation, the electrical conductivity of components and connections also plays an essential role in the functionality and efficiency of a system. Material corrosion, contamination, oxidation as well as poor compatibility of components can lead to reduced output. Early fault inspection can prevent uneconomical output. Of course, you can also find the necessary measurement technology accessories in the Bürklin Elektronik online store!
X-ray or radiographic inspection
X-ray or radiographic testing is often used in electrical engineering to detect defects and flaws inside components, soldered joints and other elements. This is because X-raying the desired electronic components provides clear information about their quality. With this inspection technique, defective parts or the finest cracks in the material can be detected non-destructively.
Ultrasonic testing
Sound waves are also used to detect faults in electrical equipment. Ultrasonic technology is often used to test the material of components for durability and quality. A probe sends high-frequency sound waves at the component after a coupling agent is applied. Reflected waves are detected and provide information about material penetration without causing damage. It can also be used to inspect installed systems.
In electrical installations such as transformers, insulators, control cabinets or relays, ultrasonic testing is used for early detection of any partial discharges. These can be caused, for example, by contamination and faulty points.
Vibration or oscillation measurement
Vibrations emanating from an electronic component have a strong informative value about its condition and quality. In the manufacturing industry, mechanical problems can be detected and corrected at a particularly early stage by observing vibrations. Vibration measuring devices detect fluctuating or special vibration characteristics and indicate, for example, imbalances and material loosening.
Flux leakage testing
Flux leakage testing is a non-destructive testing method for surface inspection by magnetizing components. Cracks, corrosion damage and the like on the ferromagnetic surface scatter field lines that are detected by the probe during scanning. High-quality test and measurement tools ensure a smooth examination process. Magnetizing and demagnetizing devices are used in a variety of ways.
In-Circuit Test (ICT)
One method of decisively testing the quality and functionality of printed circuit boards while they are still in production is the in-circuit test (ICT). Using special test adapters, the printed circuit boards can be provisionally integrated into test systems. In these systems, electrical voltage currents, correct components and functioning circuits are checked. This reduces the risk of short circuits and other faults.
Inspection technology support from the professionals
In the world of measurement and testing technology, there is a variety of control methods for analyzing technical equipment and electronic components with regard to various properties. In order to identify which methods are relevant for your individual project, it is first necessary to clarify which performance your devices and machines are to deliver in concrete terms. Bürklin Elektronik can supply you with the appropriate tools and measuring devices at any time.
Do you have questions on the subject or need support with a specific issue? Contact us and tell us about your problem! Our service team will be happy to assist you in word and deed.