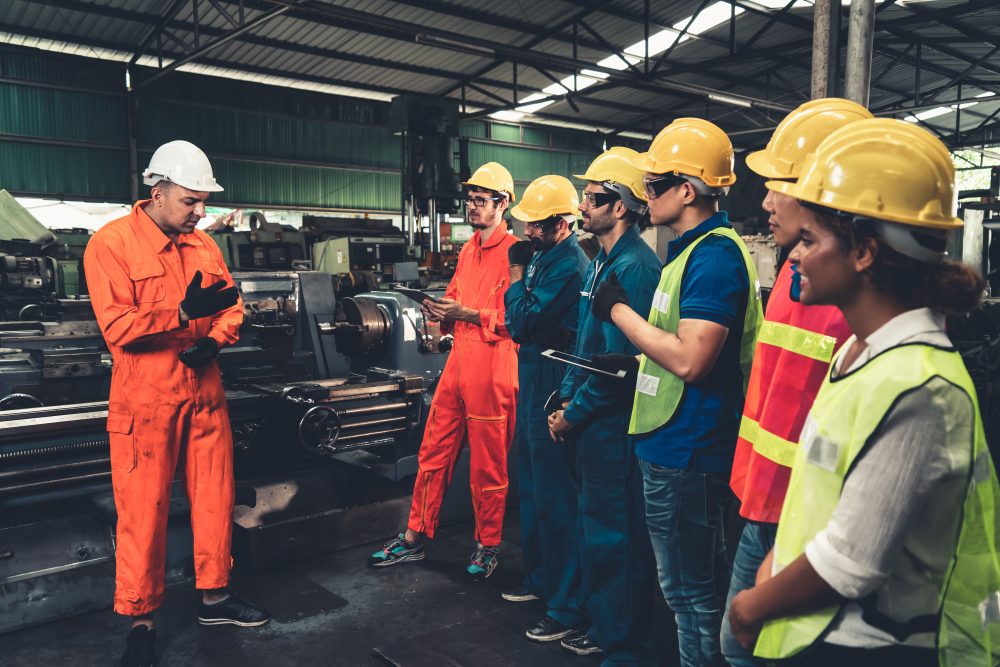
From Preventive to Predictive: A Guide for Selecting Suitable Maintenance Strategies
The maintenance of buildings, plants and machines is an essential part of operational management in many industries. Various maintenance strategies are available to companies for this purpose. What are the advantages and disadvantages of the strategies? And which strategy is best suited to your company?
What are maintenance strategies?
Maintenance strategies, also known as servicing strategies, are systematic procedures used by companies. They serve to maintain or restore the functionality of their systems, machines and infrastructure over their entire service life.
These strategies usually include defined processes, methods and guidelines aimed at minimizing operational interruptions, maximizing efficiency and safety, optimizing maintenance costs and preserving the value of the facility. They take into account factors such as the critical nature of the assets, risk management, the historical performance and reliability of equipment, operational requirements and cost efficiency.
Maintenance strategies always aim to
- Avoid unplanned downtime
- Optimize maintenance activities
- Reduce maintenance costs
- Improve the service life of equipment
Effective maintenance strategies can include preventive, predictive and condition-based maintenance approaches as well as reactive measures if necessary. The aim is to implement a tailored strategy that both reflects the operational needs of the business and provides a basis for continuous improvement and long-term asset performance.
The different maintenance strategy types
Essentially, there are four common maintenance strategies that serve to reduce operating costs, increase safety and improve overall productivity:
- Reactive or corrective maintenance
- Preventive maintenance
- Predictive maintenance
- Condition-based maintenance
- Reliability-Centered Maintenance
Reactive (corrective) maintenance
With reactive maintenance, action is only taken when a failure or malfunction occurs. This means that only measures that are necessary are carried out. These are usually repairs, replacement of components or the maintenance of defective parts.
This strategy is cost-effective in most cases, as no regular checks or premature repairs are carried out. However, this can lead to unexpected downtime, which in turn can result in higher long-term costs due to major damage.
This strategy can be useful for machines that are not critical for production, are not prone to faults and have low repair costs.
Preventive maintenance
Preventive maintenance involves regular, planned maintenance work with the aim of proactively avoiding breakdowns. Specifically, this means replacing parts, lubricating or carrying out inspections before damage occurs. These are based on defined intervals that are set out in the maintenance plan. The maintenance intervals can be time-based or usage-based.
The strategy helps to minimize downtime and increase reliability. It is particularly suitable for critical machines that must not fail. As the actual condition of the machines is not taken into account, this strategy is more inefficient and can result in unnecessary measures. It is therefore not recommended for non-critical systems.
Predictive maintenance
Predictive maintenance is a relatively new approach and is at the heart of Industry 4.0, among other things. This strategy uses real-time monitoring to predict the condition of machines, systems or devices. This makes it possible to create a maintenance plan that is as accurate as possible.
Using this strategy, maintenance and servicing work can be carried out in a targeted and efficient process. Personnel and spare parts requirements can also be scheduled more efficiently, accidents are reduced and unplanned stops become planned stops.
However, data analysis can be a challenge for companies. All machines must be connected. Older machines may need to be retrofitted with sensors in order to establish the necessary communication network.
Condition-based maintenance
This strategy uses real-time data to monitor the condition of the system. Maintenance work is only carried out when certain indicators point to a potential problem. This helps to optimize the maintenance schedule and avoid unnecessary work. This maintenance strategy uses data management to avoid the associated risks and inefficiencies of reactive and preventive maintenance.
Condition-based maintenance is particularly cost-effective. The maintenance intervals are very regular so that only defective elements are repaired or replaced. This also reduces the pressure on purchasing and saves storage space for spare parts.
Reliability-centered maintenance
Reliability-centered maintenance (RCM) is an advanced approach that focuses on the reliability of the system. It responds to non-linear failures by providing analyses of all potential failure modes and creating a plan for the stability of individual parts. However, this approach is very extensive and carries the risk that many plans are created but not successfully executed.
Total Productive Maintenance (TPM)
Total Productive Maintenance is a holistic approach that aims to maximize the overall effectiveness of systems. Every employee is involved in maintenance – from the managing director to low-level employees. This makes implementation complicated and requires a change in corporate culture.
Established processes minimize downtime and increase efficiency, quality and productivity. This not only reduces costs, but also minimizes the likelihood of customer complaints. Employees can provide useful suggestions for further improving processes.
Choosing the right maintenance strategy
To determine the most appropriate maintenance strategy, companies should first conduct a thorough assessment of their equipment, analyze the operating conditions, identify the critical components and understand the consequences of equipment failures on operations.
The cost-benefit aspects of different maintenance approaches must be weighed against each other, taking into account both short-term maintenance expenditure and long-term investment.
A company should also consider its data collection and analysis capabilities, as technologically advanced strategies such as predictive or condition-based maintenance rely on real-time data and accurate analytics.
It is also essential to involve staff in the decision-making process, as these strategies require successful implementation and commitment at all levels. Taking all these factors into account, a well-considered decision can be made that not only takes into account the specifics of the industry, but is also tailored to the specific challenges and goals of the individual company.
The maintenance plan: Your roadmap to implementing effective maintenance strategies
The maintenance plan defines how and when maintenance activities should be carried out in order to effectively implement the chosen maintenance strategy. It serves as a detailed roadmap that not only contains planned maintenance activities, but also provides guidelines for unforeseen repairs and faster response times in the event of breakdowns.
As a result, maintenance work is optimized, resources are used efficiently and the service life of equipment is maximized. At the same time, the risk of equipment failure and downtime is minimized.