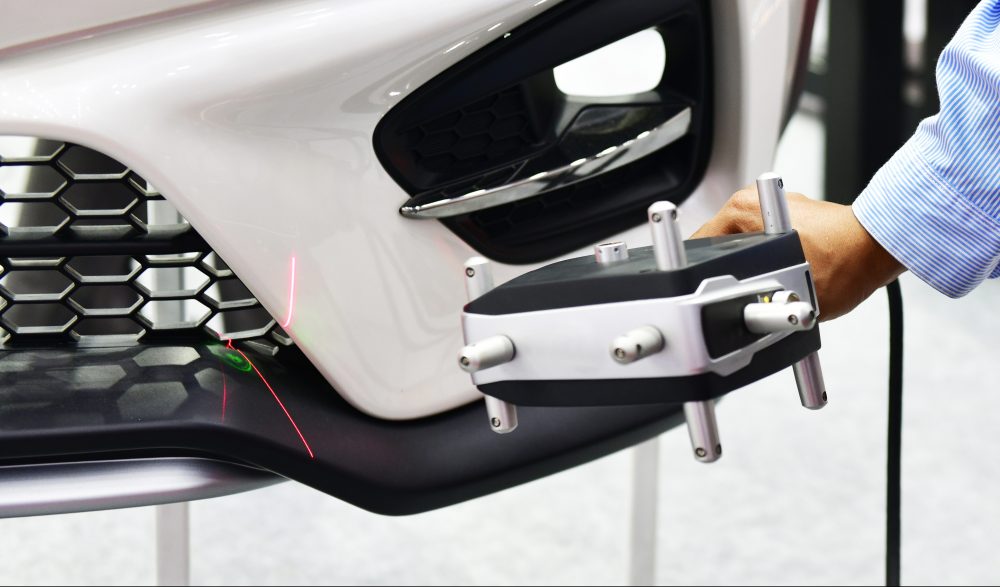
Optical Measurement Technology as a Trend in Mechanical Engineering
Optical, non-contact measurement technologies are in the fast lane and have long been just as established in mechanical engineering as tactile methods. Which method will have the edge in the future, or will both techniques be needed for ideal output? Bürklin Elektronik sheds light on the trend development and draws future-oriented conclusions.
Optical measurement – A definition
The acquisition, analysis and evaluation of complex data of a production process, a material or a plant is carried out with the help of various methods of measurement and testing technology. However, due to the nature of the examination, some procedures cause damage to the component. Optical measurement enables non-contact and non-invasive measurements thanks to the use of light signals. The technology is based on the use of optical sensors, sophisticated camera systems and other measuring devices including accessories. Using the physical absorption and reflection of light, this method can be used to measure entire surfaces instead of mere measuring points.
Optical vs. tactile measurement technology
For both technologies, there are simple and inexpensive solutions, but also professional equipment from high-priced segments. The task and degree of automation of the machine or process to be inspected are ultimately decisive in determining which technology is appropriate and to what extent. In general, however, it is clear that the higher the degree of automation, the more suitable optical measuring methods are. For maximum economic efficiency, however, it is worth weighing up the advantages and disadvantages of each method individually, or a combination.
Potentials and deficits of optical measurement technology
- Area-based measurement: Large-area optical sensors enable complete coverage of the surface of the measured object. This creates a complete digital image including detailed quality information.
- High speed due to short measurement cycles: Optical measurement systems often work in real time. They are therefore ideal for applications with short cycle times or high throughput requirements.
- Non-invasive inspection: This method also allows the measurement of sensitive or soft components without touching or damaging them.
- High flexibility: The use of different optical sensors and measurement techniques makes it possible to adapt the method to a wide range of applications and materials.
The shortcomings of optical measurement technology are primarily due to the dependence of measurability and result quality on environmental conditions. Factors such as temperature, humidity, vibrations or dust affect the accuracy of the measurements and can influence the results. Optimal measurement results therefore require controlled environmental influences. Surface conditions also have an effect: Transparent, reflective or mirroring materials only allow limited measurement.
Potentials and deficits of tactile measurement technology
- High accuracy: Due to the direct contact, tactile measurement works with particularly high precision. Information about material properties and surface texture, distances and shapes is recorded with great accuracy.
- Better robustness: External environmental influences such as dust and temperature fluctuations have hardly any effect on the measurement quality with tactile methods. As a result, the method also has high repeatability, which is important for recurring measurements or quality control.
However, tactile measurement also presents challenges. The direct contact between the measuring probe and the test object that is required here is mechanically more complex and takes a lot of time, especially with complex geometries. The probe can also cause damage or deformation to sensitive surfaces. Because it is tied to the positioning of the probe, this method is also unable to measure large surfaces. Misalignment is also a risk.
Applications of optical and tactile measurement technology
In mechanical engineering, optical measurement technology offers a wide range of applications and potential uses. It is often used for precise 3D measurement, surface inspection and waviness and roughness measurement of components. Dimensional inspection of workpieces, quality control of precision components or alignment of assemblies, on the other hand, often require direct contact. In these cases, tactile measurement is preferred.
The hybrid measurement technology as a mixed form
Because the advantages and disadvantages of the two common measurement approaches complement each other so well, a trend movement toward sensor diversity has developed. Known as hybrid metrology, this technology is pushing the use of multi-sensor measurement devices. A combination of tactile and optical measurement techniques is said to reduce the gap between measurement time and accuracy. The measurement of a larger quantity of components or even elements with more complex features is to be made possible without the procedure taking more time. Both methods can score with their advantages. Above all, optical measurement brings a gain in measurement time and relieves heavily loaded measurement systems.
For example, coordinate measuring machines can be equipped with optical measuring heads. This increases the working speed and facilitates the acquisition of touch-sensitive surfaces. Optical 3D measuring systems, on the other hand, can be expanded with switches to capture hidden areas of the component that are difficult to measure optically.
Optical measurements for quality assurance
Comparing optical and tactile measurements is like comparing apples with pears. Because: None of the methods can replace the other! Rather, an intelligent use of the techniques should be pushed according to their respective strengths. By combining both methods in the sense of hybrid measurement, quality assurance can be optimized to the maximum. Optical and tactile measuring methods are therefore not in competition with each other, but should be seen as powerful tools in a holistic approach, so that the requirements of different application areas are optimally met.